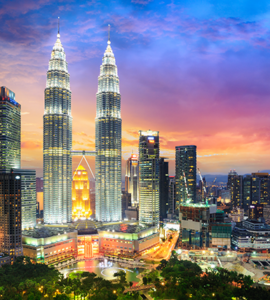
Benefits of welding machine tools
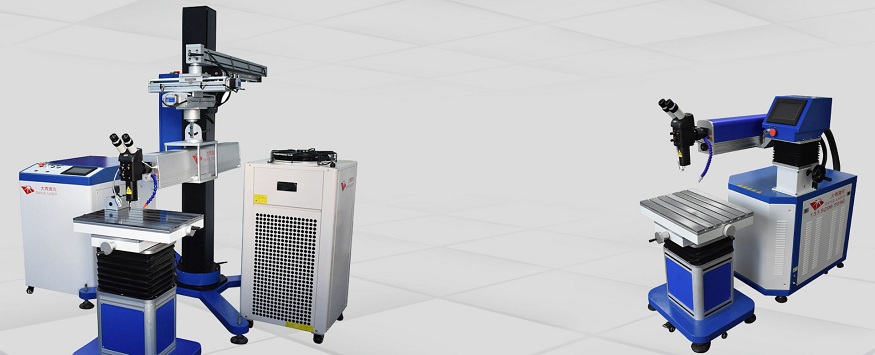
Welding, as an industrial process, is critical in the construction, manufacturing, automotive, and aerospace sectors, among others. The unsung heroes in the welding machine contractors’ tasks are weldingmachine that give them the ability to do their jobs competently and successfully. Therefore, this article aims at highlighting the advantages associated with welding machine tools and their vital role in today’s welding.
Understanding welding machine
Understanding what welding machine tools are about is a prerequisite before digging into the merits of welding machine tools. Welding machine tools comprise the equipment, machines, and devices used throughout the welding process, commencing with preparations up until the actual weld. The use of these instruments plays a crucial role in providing exact, good-quality, and safe welds. These consist of welding machines, welders, power sources, electrodes, protective gear, and other welding accessories.
Enhancing efficiency and productivity
One of the most important advantages of welding machine tools for welding machine contractors is the significant increase in efficiency and productivity. These machines enable welders to carry out their duties efficiently by reducing the amount of time and effort spent on welding. Modern welders make it possible to perform welding processes at higher speeds and deposition rates. This in turn enables welding machine contractors to work faster, accept a higher number of tasks, and increase their overall efficiency. In addition, these tools integrate state-of-the-art technology that improves the accuracy and speed of the welding process. Moreover, the advanced mechanisms and automation speed up the contractor’s ability to deliver more within a short period, resulting in increased productivity.
Ensuring Weld Quality and Consistency
Welding machine tools are vital in ensuring the quality of the weld. These machines are developed for consistent results, and they offer the exact adjustment of welding parameters. These features, such as voltage, current, and wire feed speed, can be adjusted by the welding machine contractors in order for the welds to be strong and look as expected. This level of control is crucial in ensuring that industry standards are met and in eliminating any defects in the welds. However, it is the thorough control and pinpoint accuracy of these tools that guarantee consistently superior output and even allow for individual project tweaking. To this end, precision is critical to match and, in the majority of cases, surpass highly specific industry needs.
Improving safety and operator comfort
This is because welding, by its very nature, entails the exposure of workers to electrical shocks, fumes, and UV rays, among others. The design of welding machines takes safety into account by including features like automatic switches and shielding. Moreover, such instruments usually have ergonomic designs, which improve operators’ comfort as well. Safety measures such as providing the operators with comfortable and safely designed equipment may help reduce fatigue levels, prevent accidents, and, in the end, make the workplace safer. These tools have been made to incorporate the latest safety mechanisms in order to minimize the risk of accidents in the workplace as well as improve the well-being of the welders, making them feel safer.
Versatility and adaptability
There are many types and models of welding machine tools, each designed for a particular kind of welding. Such diversity gives welding machine contractors flexibility that enables them to work on various projects and types of materials. The welding machine has machines designed for processes such as MIG, TIG, stick, and specialized processes like spot welding, among others. Adaptability plays a critical role for contractors that work with different projects and materials like steel, aluminum, and exotic alloys. The broad range of equipment ensures that the ever-changing and specific requirements of the welding industry are met. The adaptability gives contractors the opportunity to handle different welding duties, including standard and specialized applications, ensuring they can manage diverse projects with varying demands.
Energy Efficiency
Energy efficiency is a vital issue in modern society, on the one hand for ecological sustainability and, on the other, for saving costs. Energy efficiencies in most modern welding machines are highly rated, and they use less power but deliver maximum performance. This goes down on the operating costs for welding machine contractors, and this also makes the welding industry greener. The incorporation of energy-efficient technologies into such tools will reduce operational costs and be environmentally friendly, a move consistent with sustainable development trends.
Reducing material waste
There is more to efficiency in welding than time and energy. Efficiency in the utilization of resources. Automatic welding systems and robotic welders are considered welding machine tools that are programmed to minimize material waste. The weld is very clean and contains very little overfill or spatter; thus, the material consumed during each project is minimized. Reducing waste of materials also goes hand-in-hand with both cost-effectiveness and ecological sustainability. These tools are precise and automated and cut material waste while maximizing material utilization, which leads to more sustainable and eco-friendly welding methods.
Minimizing Downtime
Such downtime incurs expenses for the welding machine contractors because it affects project schedules and profits. A welding machine tool is less prone to breakdowns and malfunctions when it is well maintained. Downtime is reduced due to regular maintenance of the parts. Besides, accessibility to these parts is made easy. Reliability is very important for a project to finish within the deadline, ensuring that client satisfaction is not lost.
Meeting Industry Regulations and Standards
Welding is a regulated and standardized field where safe welds should be delivered. These requirements are aimed at supporting welding machine contractors in the welding machine tools needed to meet these requisites. Built-in quality control is also present in these instruments, which may feature live monitoring, data logging, or adherence to specific regulatory requirements for the industry.
Conclusion
Welders cannot do without machine tools and welding machine contractors. They feature several benefits, including better efficiency, productivity, quality of weld, and safety for the operator. These pieces of equipment are versatile and flexible, making it easier for contractors to take on different projects. Additionally, they are energy efficient, saving on materials. Investing in expensive welding machine tools will enable the contractors to rise above quality, abide by industry regulations, and grow steadily in the welding business for a longer time.