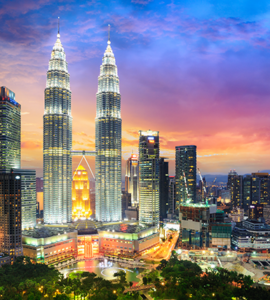
The Role of Robotics in Modern Manufacturing: Trends and Innovations

In today’s fast-paced world, the integration of robotics into manufacturing processes has become more than just a trend—it’s a necessity. Robotics, once confined to science fiction, now plays a pivotal role in driving efficiency, productivity, and innovation across various industries. This article delves into the transformative impact of robotics in modern manufacturing, exploring key trends, innovations, challenges, and future prospects.
Historical Perspective of Robotics in Manufacturing
The roots of robotics in manufacturing can be traced back to the early 20th century, with the development of the first industrial robots in the 1950s. These early robots were primarily used for tasks deemed too dangerous or repetitive for humans, such as welding and assembly line operations.
Over the decades, advancements in technology have propelled the evolution of robotics in manufacturing. From the introduction of computer numerical control (CNC) systems to the rise of collaborative robots (cobots), each innovation has contributed to greater automation, precision, and flexibility in manufacturing processes.
Key milestones in the history of the robotics industry include the introduction of the Unimate—the first industrial robot—in 1961, the development of robotic arms capable of performing complex tasks with high precision, and the integration of artificial intelligence (AI) and machine learning algorithms into robotic systems.
Current Landscape of Robotics in Manufacturing
Today, robotics is ubiquitous in modern manufacturing, with robots performing a wide range of tasks across various industries, including automotive, electronics, aerospace, and consumer goods. These tasks range from simple pick-and-place operations to sophisticated assembly and quality control processes.
Industries such as automotive manufacturing have been at the forefront of robotics adoption, leveraging robotic systems for tasks such as welding, painting, and assembly. However, other industries, including food and beverage, pharmaceuticals, and logistics, are increasingly embracing robotics to improve efficiency, safety, and product quality.
The integration of robotics into manufacturing processes has led to significant improvements in production efficiency and product quality. Robots can work continuously without fatigue, operate in hazardous environments, and perform tasks with unparalleled precision, resulting in higher throughput, reduced errors, and greater consistency in output.
Trends in Robotics Adoption in Modern Manufacturing
One of the most notable trends in robotics adoption is the rise of collaborative robots, or cobots. Unlike traditional industrial robots, cobots are designed to work alongside humans, enabling close collaboration and interaction between man and machine. Cobots are equipped with advanced safety features, such as sensors and vision systems, to ensure safe operation in shared workspaces.
Another trend shaping the future of robotics in manufacturing is the integration of artificial intelligence (AI) and machine learning algorithms. These technologies enable robots to learn from experience, adapt to changing environments, and make autonomous decisions, leading to greater flexibility, efficiency, and productivity in manufacturing processes.
The Internet of Things (IoT) is revolutionizing manufacturing by connecting robotic systems to the broader network of devices and sensors. This connectivity enables real-time monitoring, remote control, and predictive maintenance of robotic systems, enhancing reliability, uptime, and overall performance.
Innovations Driving the Future of Robotics in Manufacturing
Advances in sensing technologies, such as LiDAR, cameras, and force/torque sensors, are enhancing the capabilities of robotic systems. These sensors enable robots to perceive and interact with their surroundings more effectively, facilitating tasks such as object recognition, manipulation, and navigation.
Innovations in human-robot collaboration are making it safer and easier for humans and robots to work together. Features such as soft robotics, lightweight materials, and adaptive grippers enable robots to work alongside humans without posing a risk of injury. Additionally, safety standards and regulations ensure compliance with safety requirements in collaborative work environments.
Robotic systems are becoming increasingly customizable and flexible to meet the evolving needs of modern manufacturing. Modular designs, interchangeable end-effectors, and programming interfaces enable rapid reconfiguration and adaptation of robotic systems to new tasks, products, and production environments.
Challenges and Opportunities in Robotics Integration
While the benefits of robotics integration are substantial, the initial costs can be prohibitive for some manufacturers. However, advancements in technology, coupled with decreasing costs of robotic hardware and software, are making robotics more accessible and cost-effective for a broader range of applications and industries.
The integration of robotics into manufacturing processes necessitates upskilling and retraining of the workforce. Manufacturers must invest in training programs to ensure that employees can effectively operate, program, and maintain robotic systems. Additionally, fostering a culture of collaboration and trust between humans and robots is essential for successful integration and acceptance.
The increasing autonomy and capabilities of robotic systems raise ethical and legal concerns regarding accountability, liability, and safety. Manufacturers must navigate complex ethical and regulatory frameworks to ensure compliance with standards and regulations governing the use of robotics in manufacturing.
Conclusion
The role of robotics in modern manufacturing is rapidly evolving, driven by technological advancements, changing market dynamics, and evolving societal needs. By embracing robotics, manufacturers can unlock new levels of efficiency, productivity, and competitiveness, positioning themselves for success in the digital age. As we navigate the complexities of robotics integration, collaboration, and innovation will be key to realizing the full potential of robotics in shaping the future of manufacturing.